Introduction
An availability check enables the system to check and validate whether one or all of the required resources, whether it’s material, capacity, or production resources/tools (PRT), are available in the production process. As a production planner and scheduler, you want to have a comprehensive overview of material and capacity availability or shortage to take necessary action, if required. In case of missing component availability, the system maintains an entry in the missing parts information system. Not only this, you can also control whether the system should allow creation or release of the production order if it finds a shortage of material or capacity needed to produce the goods. Several options are available for you to perform material or capacity availability checks. You can manually check these within the production order creation screen, or you can even use a separate transaction to perform the material availability check. Alternatively, you can make the settings in the availability check for the system to perform these functions automatically.
There are three different types of availability checks in the SAP system:
Material availability check
Checks the availability of the components for the production order either against actual stocks (and optionally receipts) or against the planning.
Capacity availability check
Checks whether sufficient free capacity is available for the order’s operations.
PRT check
Checks whether the required PRT is free via a status in the master data.
The system makes availability checks during two levels:
Production order creation
Production order release
The following sequence of steps is involved in the availability checks:
- Define the checking group.
- Define the checking rule.
- Define the scope of check.
- Define the checking control.
We cover each of these steps in the following sections.
Define the Checking Group:
To set the availability checking control, follow the configuration menu path, SAP IMG Production Shop Floor Control Operations Availability Check Define Checking Group, or use Transaction OVZ2. In below , the availability (Av) 01 for Daily requirements has options to enter TotalSales and TotalDlvReqs on a daily, weekly, or monthly basis. If you select the No check checkbox, then the system switches off the available-topromise (ATP) check.
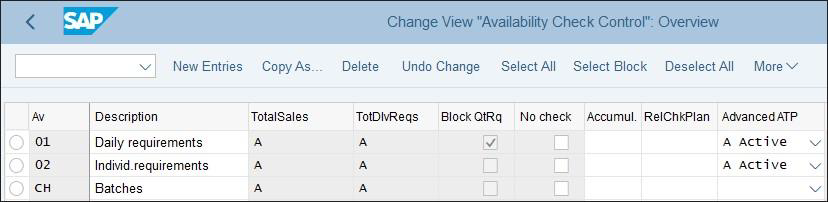
Define the Checking Rule
You can define a checking rule to cater to various functional areas such as sales and distribution (SD), MRP, production order processing, or IM. This enables you to configure and integrate different checking rules for different applications to meet your business needs. To define the checking rule, follow the configuration menu path, SAP IMG Production Shop Floor Control Operations Availability Check Define Checking Rule.
Define the Scope of Check
From the combination of the previously defined availability checking control as 01 (Daily requirements) and Checking Rule as PP, we proceed to define the scope of check. In a scope of check, you primarily define which inward and outward movements and stock types the system should consider during the availability check. For example, you can choose if the system should consider purchase orders whose GR on the delivery dates will ensure material availability. Similarly, you can set the relevant settings for the system to include (or exclude) firmed planned orders in its quantity and material availability calculation.
In the standard settings, the system only considers available unrestricted stock for the availability check; however, you may have business needs in which quality stock may also be considered as available stock during an availability check. For example, in ice cream manufacturing, the stock is kept in quality inspection even during transportation from one plant to another, until it reaches its destination. If you want to include this quality stock in the material availability check, set the relevant indicator.
To define the scope of check, follow the configuration menu path, SAP IMG Production Shop Floor Control Operations Availability Check Define Scope of Check, or use Transaction OPJJ.
In the screen shown in below Figure , you can choose the stock types and inward/outward movements that best meet the business scenarios. Scroll down and notice that in the Receipts in past field (not shown), you can control whether the system should consider all of the past and future receipts or future receipts only.
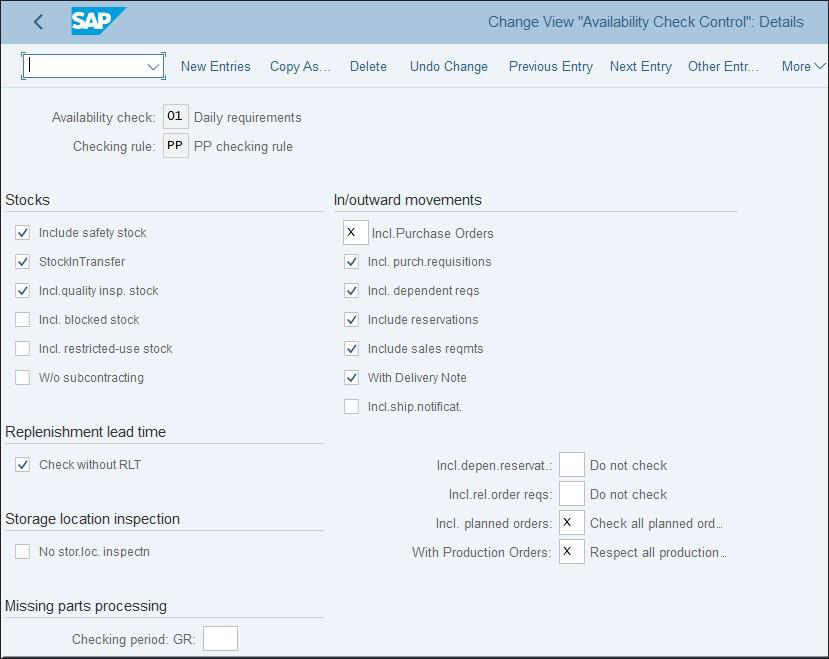
You can now proceed to assign the checking group in the MRP 3 view of the material masters for all the components in the Availability check field. For this example, use availability checking group 01, and assign it in the MRP 3 view of the material masters for all the components used in producing.
Define the Checking Control
As mentioned previously, you can maintain comprehensive availability checks of material, PRT, and capacity during production order creation and release. Because creation and release of production orders are two important business functions, you can define the level of controls for each business function. For example, if you have a long lead time between production order creation and release, you can skip some of the availability checks, such as for capacity or PRT, until you release the order. Similarly, instead of a stringent control that the system doesn’t allow the release of a production order until the material is available to produce it, you can select the option in which the user decides on releasing the production order, which meets business needs more closely so that at least partial production can commence.
To set up a checking control for production order creation and release, follow the configuration menu path, SAP IMG Production Shop Floor Control Operations Availability Check Define Checking Control, or use Transaction OPJK. In the initial screen, you’ll find several order type and plant combination entries. For this example, copy the standard settings of plant 0001 and order type PP01 and both business functions (1: creation, 2: release) to the newly created order type PP10 and for plant 1000.
The screen shown in below Figure appears after you complete the copy function.
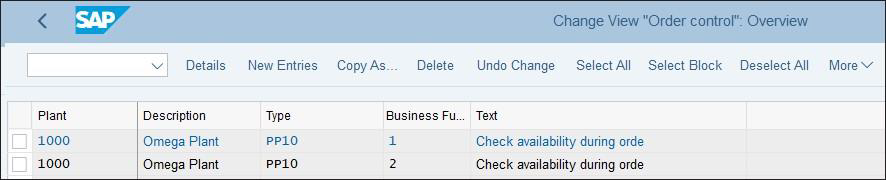